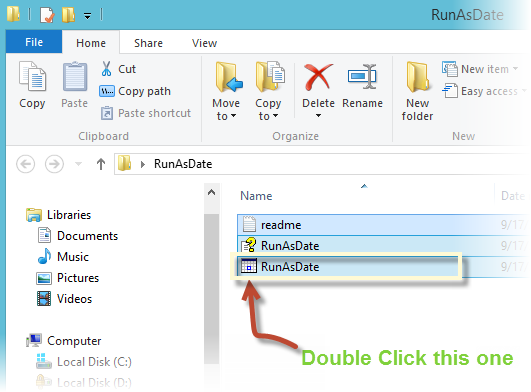
Jmatpro Crack
I had some fun today running some numbers through JMatPro, a thermodynamics simulation program similar to Thermo-Calc. You can learn a little about how these programs work on this site (I am not affiliated): [] You can use these programs to calculate the equilibrium phase fraction and wt pct in each phase. There are a variety of limitations to this method; here are some of those limitations: - It assumes that the steel is at equilibrium (the most stable state) which is often reached very slowly. Much of heat treatment is used to specifically not reach equilibrium (i.e. Martensite formation). - With high alloy steels, there are often large primary carbides left over from casting that are very difficult to get rid of through future processing.
These are often not shown in equilibrium calculations because they aren't supposed to be there anymore. - These simulations come primarily from empirical data which may not be applicable to different combinations of alloys, especially rarely used elements used together and in high amounts. That being said I have some data for you.
Distortion and Crack Prediction and Experiments in. 4 JMatPro, Sente Software Ltd. Quenched C-ring crack and the applied residual stresses during the cooling stage.
I ran these simulations at and around the common austenitizing temperatures used for these grades. I then pulled out carbide, C, Cr, and Mo wt pct at those temperature. That tells you generally what properties you will have after quenching.
For example, the amount of carbon in austenite tells you approximately what hardness can be reached and the general proportion of lath to plate martensite. The amount of Cr and Mo in solution tells you the nominal corrosion resistance, more Cr means better corrosion resistance. The amount and type of carbide controls the wear resistance, toughness, and to some extent the size of the carbides.
First let's check some numbers against known carbide volumes: [] Carbide Type and Volume Vanadium Niobium Chromium Total CPM S35VN 3.0% 0.5% 10.5% 14.0% CPM S30V 4.0% 10.5% 14.5% 440C 0% 12.0% 12.0% 154 CM 0% 17.5% 17.5% Here are the numbers I got for S35VN, S30V, 440C, and 154CM: The carbide numbers are actually pretty close. The biggest deviation is 154CM, which is quite a bit higher in Crucible's numbers than the JMatPro calculations.
None of these simulations should be taken as gospel. Some are close and some are going to be off. But as an approximation they're probably not too bad. Installing haproxy on windows. Based on these numbers we would expect these steels to have comparable toughness but the V grades would have superior wear resistance because of harder MC carbides. Here are some low carbide stainless steels: Speaking to Sandvik, they said that 14C28N has a little bit higher carbide volume than 13C26, they said that they knew they were at the edge of the carbide volume range for avoiding primary carbides.

However, in these calculations, JMatPro predicts lower carbide volume for 14C28N. The numbers aren't perfect. You can see that 19C27 and Niolox have somewhat intermediate carbide volumes, though Niolox carbides may be somewhat smaller because of the niobium addition. I haven't seen any micrographs that confirm that fact.
Both of those steels are also on the low end of Cr in solution. JMatPro predicts a little higher C in solution for 19C27, and a little lower for Niolox, which seems to fit with the achievable hardness for those grades. Elmax looks terrible here, with lots of chromium carbides, very little MC, and low achievable hardness and corrosion resistance. D2 has medium-high carbide volume, but in practice is even higher because of the very persistent primary carbides in D2. Vanadis 4 Extra looks pretty good being a PM grade with a medium amount of carbide and all of it being predicted to be MC carbide, which is why it has such a good combination of toughness and wear resistance. The MC carbides being harder than chromium carbides means much better wear resistance while the difference in toughness is negligible. Captain tsubasa 1983 1 to 128 nonton sub indo. The PM process allows a little higher carbide volume than conventionally cast while maintaining good toughness and edge stability, but edge stability is still worse than AEB-L/13C26 or 52100 with their 3% carbide.